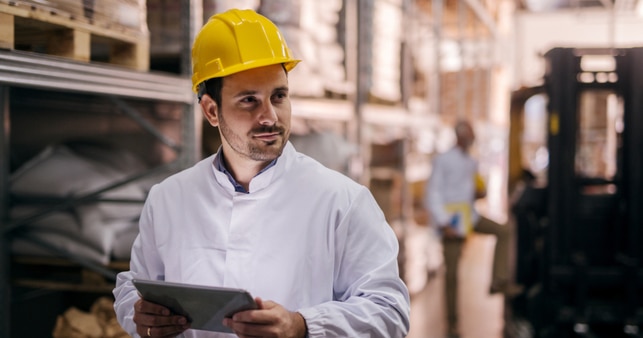
A risk assessment is a systematic process of evaluating the potential risks that may be involved in an activity, especially in terms of workplace health and safety. There are generally three major questions which are asked when conducting a risk assessment:
What hazards exist that may cause harm?
How severe would the harm be?
How likely is the harm to occur?’
Once this evaluation is made, the next step is to consider what could be put in place to either eliminate or reduce the risk as much as possible.
Why is risk assessment important?
A risk assessment ensures that you are able to identify all hazards in the workplace which may lead to an injury or illness. Once risks are identified, the business is then able to review the best measures to eliminate the risk completely or implement control measures to minimise the likelihood of an injury/illness occurring.
Risk assessments are highly important as they can assist to:
create awareness of hazards and risks
identify who may be at risk
determine whether there are existing and adequate control measures in place
What is the purpose of a risk assessment?
The purpose of a risk assessment is to identify hazards in the workplace in order to implement control measures that can eliminate or minimise risks as much as possible. This, in turn, will help with providing a safer working environment.
Risk assessments should be completed in consultation with workers. This will assist in identifying hazards which may normally go unnoticed.
What are the benefits of a risk assessment?
The greatest benefit of a risk assessment is ensuring safety within your workplace. A comprehensive risk assessment may prevent, or in the very least minimise, workplace injuries or illnesses. Other benefits of risk assessments may include:
Cost-saving
The right control measures should reduce injuries or illnesses occurring in the workplace, which will cause a reduction in workers compensation claims, absenteeism, and reactive measures.
Employee loyalty
Placing a strong emphasis on risk assessments may convey to your employees that you take their safety seriously. This can result in greater loyalty from their end.
How to conduct a risk assessment?
While there are many different ways to capture risk in the workplace, generally a risk assessment will have four steps:
Step 1: Identify Hazards
Thoroughly assess the workplace to identify hazards – both existing and potential. This can be completed by creating a list of hazards and current control measures the business has in place.
It is always good practice to consult your employees in this stage. Your employees are directly encountering these hazards – consulting them can shed invaluable and in-depth insights.
Step 2: Assess the risk
Once the hazards have been identified, the degree of risk they present needs to be determined. This entails pre-empting how these hazards can cause potential injury in different situations and conditions.
During this step, the business should consider how likely it is that someone will be harmed and how serious the resulting injury may be. In this stage, we should also consider if the current control measures the business have in effect are reducing risk.
Step 3: Control the risk
After conducting a thorough assessment of the risk, the business should then look at processes to eliminate or reduce the risk as much as possible. The business should use the hierarchy of control measures to do this.
This starts with elimination as the first option and works through the different options to the lowest control which is personal protective equipment (PPE). It should be noted that the PPE should be one of the last considerations when reviewing risks.
Step 4: Review
The business should review the effectiveness of the control measures once it has been implemented. In this step we should consider if the measure is fit for the purpose it is used for; is it suitable for the nature of the work? Or if something has been installed, has it been set up correctly?
Review is an ongoing process, in the event something new is introduced into the environment the business may need to consider if their control measure is the most effective for their business.
Join 27,000 Business Owners.
Free Business Resources and Expert Advice 24/7 to Make Your Workplace Better.
Frequently Asked Questions
Who is responsible for risk assessments in the workplace?
Everyone is responsible for risk assessments in the workplace. The management team should start the process and discuss risks with workers. In fact, consulting with workers during each step of the risk management process is a crucial aspect.
What is the difference between a JSA and risk assessment?
The key difference between the two is the nature of what they are assessing. The purpose of a risk assessment is to identify hazards and its risks across the workplace. This is then followed by counteracting safeguards and control measures. A Job Safety Analysis (JSA), on the other hand, concentrates on risks that are job-specific. JSAs are conducted on tasks – rather than workplaces – and are evaluated on a step-by-step basis.
Is a SWMS the same as a JSA?
No, however, they can be quite similar in nature.
A Job Safety Analysis (JSA) is a form of risk assessment that provides step by step details on the process to carry out a task in the workplace. The three main components of this is to outline the task, hazards, and control measures – including step by step instructions on how to carry out the task by controlling the hazard. A JSA can be completed on most tasks and is not limited to high risk construction work.
A Safe Work Method Statement (SWMS) also provides details of a step by step process to complete a task. A SWMS is required for high-risk construction work only. The process requires an identification of work that is high risk, listing the hazards, the control measures, and how the control measures are implemented.
When should you do a risk assessment?
Risk assessments should be conducted periodically to ensure that the preceding assessment is still applicable. Between the scheduled periods, risk assessments should also be conducted in response to certain scenarios. This includes a workplace accident/incident, when a new task has been introduced to the worksite, during periods of high staff turnover, and if new equipment has been introduced to the workplace.
What are the basic principles of risk management?
There are four basic principles that form the framework of risk management. First and foremost, hazards need to be identified. You cannot manage hazards if you are unsure of what they are. They then have to be assessed. You have to understand and pre-empt the different types of risks that could potentially arise from a hazard.
The third principle is initiating safety measures and controls to either overcome or minimise the risk. And the final principle is reviewing the hazard and measures that have been put in place and adjusted if necessary.
What is a risk assessment form?
A risk assessment form is a document where the process of risk assessment can be documented – including information around hazards and risks in a workplace, as well as the control measures that can be put in place to eradicate or minimise them. This form can then be used as a point of reference for anyone involved in the job to familiarise themselves with the work ahead of them – functioning as a precautionary step.
What is the process of risk analysis?
The first step is to identify hazards – study your worksites and identify its risks. Following that, you need to assess the risks, consider how likely an injury/illness can occur and how serious this can be. This involves reviewing any control measures currently in place. Once the assessment has been conducted, safeguards need to be put in place, and regularly reviewed, to control the risks.
What are the risks of manual handling?
The most common risk associated with manual handling is musculoskeletal disorders (MSDs). This disorder may include back injuries, sprains and strains, soft tissue injuries, joint and bone injuries, and more.
MSDs can occur over time due to gradual wear and tear or continuous use of the same body parts, or it could be sudden because of unexpected movement or strenuous activity.
What is a manual handling risk assessment?
A manual handling risk assessment is a risk assessment which targets manual handling. Manual handling refers to tasks where an individual is subject to lifting, lowering, pushing, pulling carrying, holding or restraining an object. It is generally linked to repetitive movements, repetitive or sustained force, high or sudden force, sustained or awkward postures, or exposures to vibration.
Like any assessment, the purpose of this is to identify the hazards and assess the risk before risk control measures are put in place to eliminate or reduce the risk as much as possible.
What is the best way to prevent injury from a manual handling task?
There is no one size fits all approach to preventing injury. Safework Australia recommends the best and most cost-effective way to remove or minimise risk of injuries such as musculoskeletal disorders (MSD) is to review the task and risks when planning out the job.
During this stage, all hazards and risks can be “designed out” before they are introduced. This indicates that when purchasing equipment and reviewing the staff, the business should consider equipment which is designed to reduce the risk from the outset.
On top of this, risk assessments should always be conducted and control measures should be implemented accordingly, and reviewed regularly.
What is the difference between hazard and risk?
A hazard refers to situations, materials or objects that have the potential to cause harm. For example, working with chemicals or jobs that involve heights. Risk, on the other hand, refers to the potential consequence (injury or damage) resulting from a hazard. As such, a particular hazard can be considered ‘low-risk’ or ‘high-risk’.
What is the purpose of the hazard analysis?
A hazard analysis is very useful to minimise workplace injuries and incidents. Through the analysis, hazards in the workplace get brought to light that may have otherwise gone unnoticed. The exercise of conducting a hazard analysis also evaluates the causes behind specific hazards. This can provide insights that can be used in implementing control measures and safeguards – making the hazard lower in risk.
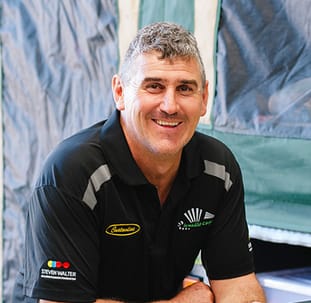
Get Workplace Advice Now
Call Our Team of Expert Advisers Who Will Help You with Your Workplace Questions.